The Scientific Research Behind Porosity: A Comprehensive Guide for Welders and Fabricators
Understanding the complex mechanisms behind porosity in welding is essential for welders and producers aiming for flawless craftsmanship. As metalworkers explore the depths of this phenomenon, they uncover a globe controlled by numerous aspects that influence the formation of these small voids within welds. From the composition of the base materials to the intricacies of the welding process itself, a plethora of variables conspire to either intensify or relieve the existence of porosity. In this detailed overview, we will certainly untangle the scientific research behind porosity, discovering its effects on weld top quality and introduction advanced methods for its control. Join us on this journey via the microcosm of welding flaws, where precision meets understanding in the search of remarkable welds.
Comprehending Porosity in Welding
FIRST SENTENCE:
Evaluation of porosity in welding reveals vital insights into the honesty and quality of the weld joint. Porosity, identified by the presence of tooth cavities or voids within the weld metal, is an usual concern in welding processes. These spaces, otherwise correctly resolved, can compromise the structural honesty and mechanical homes of the weld, bring about potential failures in the completed item.
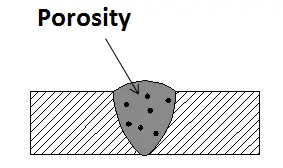
To identify and evaluate porosity, non-destructive screening techniques such as ultrasonic screening or X-ray examination are often employed. These techniques enable the identification of interior issues without compromising the integrity of the weld. By analyzing the size, shape, and circulation of porosity within a weld, welders can make enlightened decisions to enhance their welding processes and accomplish sounder weld joints.
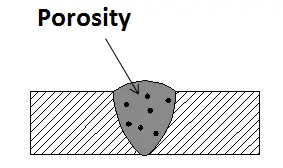
Variables Affecting Porosity Development
The event of porosity in welding is influenced by a myriad of variables, ranging from gas securing efficiency to the details of welding criterion settings. Welding criteria, including voltage, present, travel speed, and electrode kind, also influence porosity formation. The welding method employed, such as gas metal arc welding (GMAW) or secured steel arc welding (SMAW), can influence porosity development due to variations in warm circulation and gas protection - What is Porosity.
Impacts of Porosity on Weld Quality
Porosity formation significantly jeopardizes the structural honesty and mechanical homes of bonded joints. When porosity is present in a weld, it creates spaces or dental caries within the material, reducing the general stamina of the joint. These voids function as tension concentration factors, making the weld more susceptible to fracturing and failing under load. The presence of porosity likewise deteriorates the weld's resistance to rust, as the entraped air or gases within deep spaces can react with the surrounding environment, resulting in deterioration gradually. In addition, porosity can impede the weld's capacity to hold up against stress or influence, more jeopardizing the overall high quality and dependability of the bonded framework. In essential applications such as aerospace, auto, or architectural building and constructions, where safety and resilience are extremely important, the detrimental effects of porosity on weld top quality can have extreme effects, stressing the value of lessening porosity via correct welding methods and procedures.
Techniques to Reduce Porosity
Additionally, using the suitable welding criteria, such as the proper voltage, current, and take a trip his explanation speed, is vital in protecting against porosity. Maintaining a consistent arc size and angle during welding also assists minimize the chance of porosity.

Utilizing the suitable welding technique, such as back-stepping or using a weaving movement, can also aid disperse heat equally and minimize the possibilities of porosity development. By carrying out these methods, welders can successfully minimize porosity and generate top notch welded joints.

Advanced Solutions for Porosity Control
Applying sophisticated innovations and ingenious techniques plays a critical duty in accomplishing superior control over porosity in welding procedures. One advanced solution is the usage of advanced gas see this page blends. Shielding gases like helium or a combination of argon and hydrogen can help in reducing porosity by supplying far better arc security and improved gas protection. Additionally, utilizing innovative welding methods such as pulsed MIG welding or changed environment welding can likewise help alleviate porosity concerns.
Another sophisticated solution involves the usage of innovative welding equipment. For example, using equipment with built-in features like waveform control and sophisticated source of power can boost weld quality and decrease porosity dangers. The execution of automated welding systems with specific control over criteria can dramatically minimize porosity defects.
Furthermore, including innovative surveillance and examination modern technologies such as real-time X-ray imaging or automated ultrasonic screening can help in identifying porosity early in the welding procedure, enabling prompt rehabilitative actions. In general, integrating these innovative options can substantially enhance porosity control and improve the overall top quality of bonded components.
Conclusion
In conclusion, comprehending the science behind porosity in welding is necessary for welders and fabricators to generate top quality welds - What is Porosity. Advanced remedies for porosity control can further boost the welding process and see this site make sure a solid and reputable weld.